概述
循环流化床发电技术(CFBC)是指小颗粒的煤与空气在炉膛内处于沸腾状态下,即高速气流与所携带的稠密悬浮煤颗粒充分接触燃烧的技术。
循环流化床燃烧方式的特点是:
1. 清洁燃烧,脱硫率可达80%-95%,NOx排放可减少50%;
2. 燃料适应性强,特别适合中、低硫煤;
3. 燃烧效率高,可达95%-99%;
4. 负荷适应性好,负荷调节范围30%-100%。
循环流化床锅炉煤种适应性广,是当前世界上煤炭洁净燃烧的首选炉型,具有氮氧化物排放低、燃料适应性广、燃烧效率高、脱硫率可达到98%、排出灰渣易于综合利用、负荷调节范围大等突出的高效低污染优点,是重要的洁净燃烧技术。
技术原理
1. 循环流化床锅炉的结构和作用
循环流化床锅炉脱硫是一种炉内燃烧脱硫工艺,以石灰石为脱硫吸收剂,燃煤和石灰石自锅炉燃烧室下部送入,一次风从布风板下部送入,二次风从燃烧室中部送入。石灰石受热分解为氧化钙和二氧化碳。气流使燃煤、石灰颗粒在燃烧室内强烈扰动形成流化床,燃煤烟气中的SO2与氧化钙接触发生化学反应被脱除。为了提高吸收剂的利用率,将未反应的氧化钙、脱硫产物及飞灰送回燃烧室参与循环利用。钙硫比达到2-2.5左右时,脱硫率可达90%以上。
锅炉采用单锅筒,自然循环方式,总体上分为前部及尾部两个竖井。前部竖井为总吊结构,四周有膜式水冷壁组成。自下而上,依次为一次风室、浓相床、悬浮段、蒸发管、高温过热器、低温过热器及高温省煤器。尾部竖井采用支撑结构,由上而下布置低温省煤器及管式空气预热器。两竖井之间由立式旋风分离器相连通,分离器下部联接回送装置及灰冷却器。燃烧室及分离器内部均设有防磨内衬,前部竖井用敖管炉墙,外置金属护板,尾部竖井用轻型炉墙,由八根钢柱承受锅炉全部重量。
锅炉采用床下点火(油或煤气),分级燃烧,一次风率占50%-60%飞灰循环为低倍率,中温分离灰渣排放采用干式,分别由水冷螺旋出渣机、灰冷却器及除尘器灰斗排出。炉膛是保证燃料充分燃烧的关键,采用湍流床,使得流化速度在3.5—4.5m/s,并设计适当的炉膛截面,在炉膛膜式壁管上铺设薄内衬(高铝质砖),即使锅炉燃烧用不同燃料时,燃烧效率也可保持在98%-99%以上。
分离器入口烟温在450度左右,旋风筒内径较小,结构简化,筒内仅需一层薄薄的防磨内衬(氮化硅砖)。其使用寿命较长。循环倍率为10-15左右。
循环灰输送系统主要由回料管、回送装置,溢流管及灰冷却器等几部分组成。
床温控制系统的调节过程是自动的。在整个负荷变化范围内始终保持浓相床床温860度的恒定值,这个值是最佳的脱硫温度。当自控制不投入时,靠手动也能维持恒定的温床。
2. 循环流化床锅炉节能改造技术
1. 加装燃油
经燃油节能器处理之碳氢化合物,分子结构发生变化,细小分子增多,分子间距离增大,燃料的粘度下降,结果使燃料油在燃烧前之雾化、细化程度大为提高,喷到燃烧室内在低氧条件下得到充分燃烧,因而燃烧设备之鼓风量可以减少15%至20%,避免烟道中带走之热量,烟道温度下降5℃至10℃。燃烧设备之燃油经节能器处理后,由于燃烧效率提高,故可节油4.87%至6.10%,并且明显看到火焰明亮耀眼,黑烟消失,炉膛清晰透明。彻底清除燃烧油咀之结焦现象,并防止再结焦。解除因燃料得不到充分燃烧而炉膛壁积残渣现象,达到环保节能效果。大大减少燃烧设备排放的废气对空气之污染,废气中一氧化碳(CO)、氧化氮(NOx)、碳氢化合物(HC)等有害成分大为下降,排出有害废气降低50%以上。同时,废气中的含尘量可降低30%-40%。安装位置:装在油泵和燃烧室或喷咀之间,环境温度不宜超过360℃。
2. 安装冷凝型燃气锅炉节能器
燃气锅炉排烟中含有高达18%的水蒸气,其蕴含大量的潜热未被利用,排烟温度高,显热损失大。天然气燃烧后仍排放氮氧化物、少量二氧化硫等污染物。减少燃料消耗是降低成本的最佳途径,冷凝型燃气锅炉节能器可直接安装在现有锅炉烟道中,回收高温烟气中的能量,减少燃料消耗,经济效益十分明显,同时水蒸气的凝结吸收烟气中的氮氧化物,二氧化硫等污染物,降低污染物排放,具有重要的环境保护意义。
3. 采用冷凝式余热回收锅炉技术
传统锅炉中,排烟温度一般在160-250℃,烟气中的水蒸汽仍处于过热状态,不可能凝结成液态的水而放出汽化潜热。众所周知,锅炉热效率是以燃料低位发热值计算所得,未考虑燃料高位发热值中汽化潜热的热损失。因此传统锅炉热效率一般只能达到87%-91%。而冷凝式余热回收锅炉,它把排烟温度降低到50-70℃,充分回收了烟气中的显热和水蒸汽的凝结潜热,提升了热效率;冷凝水还可以回收利用。
4. 锅炉尾部采用热管余热回收技术
余热是在一定经济技术条件下,在能源利用设备中没有被利用的能源,也就是多余、废弃的能源。它包括高温废气余热、冷却介质余热、废汽废水余热、高温产品和炉渣余热、化学反应余热、可燃废气废液和废料余热以及高压流体余压等七种。根据调查,各行业的余热总资源约占其燃料消耗总量的17%-67%,可回收利用的余热资源约为余热总资源的60%。
3.超临界循环流化床锅炉
根据中国的情况,在未来的相当长的时间内,新安装的煤粉炉将主要是高效率、低煤耗的超临界和超超临界机组,加上烟气处理系统使其排放达标。这些新的超临界煤粉炉机组在经济上、性能上和排放上均比亚临界的循环流化床锅炉更具有竞争性。因此,循环流化床锅炉面临着提高发电效率的挑战。超临界参数发电在发电效率方面具有优势。超临界循环流化床锅炉就是将超临界直流锅炉技术与CFB锅炉相结合。循环流化床(CFB)燃烧技术有着燃料适应性广、污染排放低、负荷调节比大、灰渣利用率高等优点,近年来取得了快速的发展。超临界循环流化床(SCFB)兼具了CFB燃烧技术和超临界蒸汽循环的特点,是一种高效清洁燃煤发电技术,商业前景广阔。大型超临界CFB锅炉技术综合了低成本污染控制和高供电效率两方面优势,是循环流化床锅炉的发展方向。
600 MW超临界CFB锅炉设有中隔墙、双布风板大炉膛、6个循环回路,布局如下图所示,设计具有挑战性。气固流场、传热、水动力、稳定性,如大炉膛双布风板支腿密相区颗粒混合问题、床料平衡与控制问题,高炉膛气固浓度分布,二次风穿透问题,悬吊受热面表面颗粒流动问题,6分离器循环回路物料平衡问题,炉膛水冷壁、中隔墙和悬吊受热面的热流分布规律,超临界水动力特性,回料系统受阻对炉膛运行的影响等问题,是600MW超临界循环流化床锅炉设计和运行中至关重要和必须解决的问题。
600 MW超临界CFB锅炉设有中隔墙、双布风板大炉膛、6个循环回路,布局如下图所示,设计具有挑战性。气固流场、传热、水动力、稳定性,如大炉膛双布风板支腿密相区颗粒混合问题、床料平衡与控制问题,高炉膛气固浓度分布,二次风穿透问题,悬吊受热面表面颗粒流动问题,6分离器循环回路物料平衡问题,炉膛水冷壁、中隔墙和悬吊受热面的热流分布规律,超临界水动力特性,回料系统受阻对炉膛运行的影响等问题,是600MW超临界循环流化床锅炉设计和运行中至关重要和必须解决的问题。
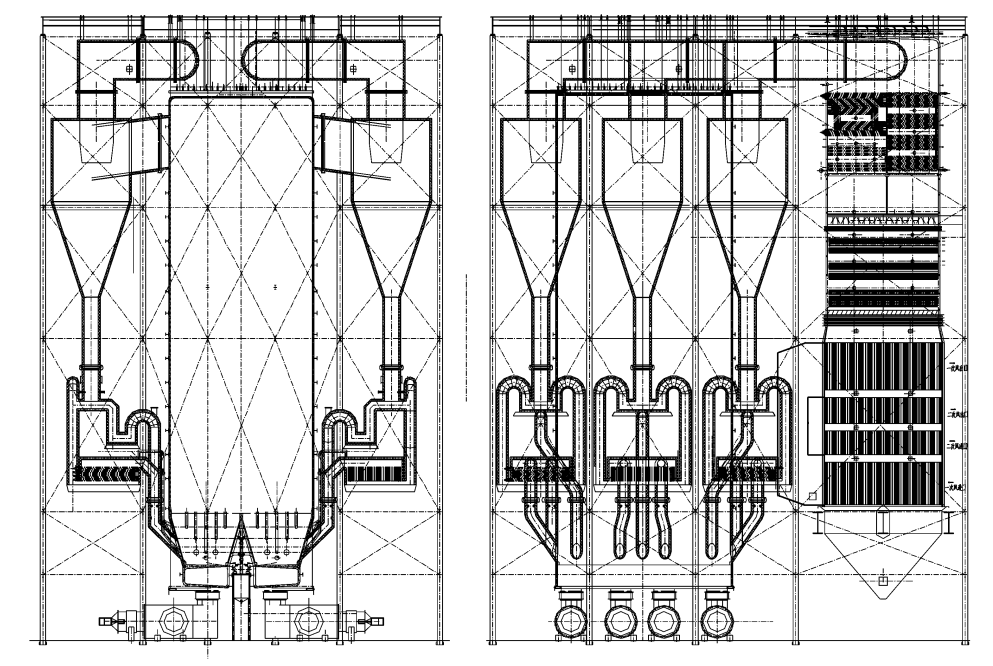
国内发展和应用现状
我国的CFBC技术开发工作始于八十年代中期,由中科院工程热物理所、清华大学、浙江大学和哈尔滨工业大学等单位组织开发研制的循环流化床锅炉分别于九十年代相继投入运行,最大容量达到了75t/h。主要技术类型有:百叶窗式、热旋风筒式、平面流分离器式等。目前国内已具备设计、制造75t/h及以下的小型CFBC锅炉的能力,但在工艺及辅机配套、连续运行时间、负荷、磨损、漏烟、脱硫等技术方面还有待完善。已投入运行的CFBC锅炉大部分未实施石灰石脱硫,燃烧室运行温度大多高于900℃。国家经贸委组织的75t/h循环流化床锅炉完善化示范工程,先后完成两种完善化炉型的设计、制造、安装和试验,于1996年初陆续投入运行。
四川内江电厂引进了芬兰奥斯龙公司100MW循环流化床锅炉已于1996年6月投产。50MW(220t/h)循环流化床锅炉纳入“八五”科技攻关,完成了设计和制造,1996年开始安装调试,目前项目工作尚未结束。国内已基本具备设计、制造50MWCFBC锅炉的能力。
1997年,通过鉴定或工程验收的有:清华大学、四川锅炉厂承担的四川湔江水泥厂75t/h循环流化床锅炉完善化工程;中科院工程热物理所分别与杭州锅炉厂、济南锅炉厂、无锡锅炉厂联合承担的75t/h循环流化床锅炉完善化或研究制造。在循环流化床燃烧技术大型化方面取得突破的“甘肃窑街煤电公司130吨/小时循环流化床锅炉示范项目”,目前已顺利通过验收。
清华大学开发的循环流化床等洁净煤技术能有效地解决燃煤造成的环境污染问题。循环流化床锅炉具有在800-900℃条件下稳定运行,能烧劣质煤并能高效脱硫三大优点。燃煤电厂采用这种设备,既能节约优质煤,又能减少二氧化硫和氮氧化物排放,还能降低发电成本,具有良好的环保效益和经济效益,非常适合我国国情。
清华大学实验室开发的130吨/小时循环流化床锅炉2001年初在秦皇岛北山发电厂成功应用;220吨/小时循环流化床锅炉已在山东威海热电厂进行建设并已投入运营;425吨/小时循环流化床锅炉的研发也被列入了科技部“十五”攻关计划。我国在循环流化床锅炉科技开发方面已取得了良好的成果,但是,由于缺乏资金,国产流化床锅炉的进一步开发困难重重。
循环流化床锅炉通常是先从小型锅炉厂开始,进行技术运用和试验,再逐步推广到中型、大型锅炉厂,如东方电气(四川)、上海电气等企业,进入大规模的生产环节中。目前,相关技术已经通过企业推向市场。现在,循环流化床燃煤发电已经占了我国燃煤发电总量的近20%。
我们国家高度重视超临界循环流化床锅炉的发展,先后在2个国家科技攻关中资助相关的前期研究 ,跟踪国际上的最新发展动态。在2002年的国家高技术研究发展计划( 863)中,设立了超临界循环流化床锅炉研究 ( 2002AA529100)项目,由清华大学和哈尔滨锅炉厂共同承担。在该项目中,形成了 800MWe 超临界循环流化床锅炉方案,围绕超临界循环流化床锅炉的若干关键问题,展开了详细的研究 。在此基础上,完成了自行设计的 600 MW 超临界循环流化床锅炉设计 。
国外发展和应用现状
CFBC技术在发达国家得到大力开发,技术成熟,正向大型化发展。目前单机容量最大的CFBC锅炉(250MW,蒸发量700t/h)电站已在法国投入运行,锅炉效率90.5%,脱硫率93%,NOx排放低于250mg/Nm3按技术特点分为以下几个技术流派:以Lurgi公司为代表的带有外置换热床采用热旋风分离器的循环床;以德国B&W公司为代表的塔式布置中温旋风分离循环床技术;美国福斯特惠勒公司发展的汽冷旋风筒分离器带有INTREX副床的循环床技术等。锅炉容量等级有50t/h、100t/h、400t/h,最大单机容量CFBC锅炉(250MW,蒸发量900t/h)电站已在法国投入运行,ABB-CE也在设计1500t/h的CFBC锅炉。目前全世界12MW以上的CFBC锅炉运行约300台,其中40%在美国,40%在欧洲,20%在亚洲。最长运行时间达到9万小时,最长连续运行时数为13个月,负荷率一般可达90%以上。
由于超临界循环流化床锅炉的优势,法国电力公司( EDF)非常看好这一技术 , 委托 FW 公司进行600 MW 超临界直流锅炉的设计研究,主蒸汽参数为31 MPa、593 ℃。对超临界循环流化床直流锅炉的分析表明, 该技术的发展前景非常乐观 。因此美国和欧洲相继开展了更高参数的循环流化床直流锅炉的研究开发 。在美国的能源部资助下, FW公司进行了参数分别为① 400 MW/ 31 . 1 MPa 593 ℃ 593 ℃;② 600 MW/31 . 1 MPa 593 ℃593 ℃; ③ 600 MW/ 37 . 5 MPa 700 ℃ 700 ℃的超超临界参数的循环流化床锅炉研究开发 。由来自芬兰、德国、希腊和西班牙的 6 家公司合作研究 800 MW ( 30 . 9 MPa 604 621 ℃)。设计中采用采用 INTREX ,共 12 个,其中 8 个布置第三级和末级过热器 , 4 个布置末级再热器 , 并对再热蒸汽温度进行调节 。设计排烟温度为 90 ℃,凝汽器采用 18 ℃的海水作为循环水, 从而使得该机组的循环效率达45 %。Alstom、 ABB 公司的研究也比较早, 但由于没有落实工程,研究进展不大。.
供应商信息
HOVAL瑞士集团公司
河北华倬锅炉集团有限公司
河南开封得胜锅炉股份有限公司
长春市鼎新锅炉制造有限责任公司
青岛嘉能海诺电力设备有限公司
济南热源循环流化床锅炉配件制造有限公司
太原锅炉集团有限公司工业锅炉厂
经典案例
引进循环流化床燃烧先进技术秦皇岛北山电厂摆脱困境
由清华大学开发的我国第一台具有自主知识产权的130t/h水冷异形分离循环流化床锅炉,近日在河北省秦皇岛北山发电厂通过72小时试运行,正式并网发电。这标着我国循环流化床燃烧技术在向大型化发展方面取得重要突破。
国家煤清洁燃烧工程研究中心的岳山溪教授介绍说,循环流化床燃烧技术是目前国际上商业化程度最好的清洁煤燃烧技术之一,具有煤种适应性强、负荷调节范围大、燃烧稳定、炉内脱硫和分级燃烧有效降低污染物排放等优点,突出特点是可燃烧劣质煤和煤矸石。
秦皇岛北山发电厂始建于20世纪70年代,原设计燃烧锅炉为煤粉炉,发电成本一直较高。2000年4月,在国家经贸委等有关部门的支持下,该厂充分利用当地丰富的劣质煤和煤矸石资源,引进了清华大学开发的水冷异形分离循环流化床技术进行技术改造,实现了当年施工当年投产。该厂技术改造完成后,每年可“吃”掉发热量在3000大卡以下的劣质煤42万吨,发电成本也将从每千瓦时0.30元降至0.25元以下,既解决了自身的发展问题,又解决了当地煤炭企业的出路问题。同时先进工艺极大地降低了二氧化硫和氮氧化物的排放量,排出的灰渣也全部被当地水泥厂包购,从而使秦皇岛北山发电厂成为一个节能增效综合利用的环保型发电厂。
《中国环境报》2001-1-23第一版
循环流床锅炉技术的应用
秦皇岛市北山发电厂是建于世纪年代初的国有企业,现有装机容量49kW,是一座坑口电站。该电厂按照设计煤种即75%的山西大同煤加25%当地柳江煤(热值较低)燃用,需耗用大量优质燃料,运行费用较高。该厂于2000年底采用130t/h循环流化床锅炉(清华大学专利技术,由四川锅炉厂制造)替代原有的燃用优质燃料且污染严重的煤粉炉,新锅炉可全部燃用柳江煤矿的劣质煤,同时循环流化床锅炉燃烧的灰渣还可被周围众多的水泥厂综合利用。该项目既盘活了国有资产,又采用取得了显著的经济效益,同时也减少了污染气体的排放,极大地改善了环境。
项目总投资:190万
节能效果:年节能效益172.89万元,年减排CO23.83万t。
投资回收期:1.1年
——《最佳节能实践案例》 P143
东方电气集团东方锅炉自主研制的世界首台最大容量的600MW超临界循环流化床锅炉成功投运
2013年4月14日8点12分,东方电气集团东方锅炉股份有限公司自主研制的世界首台最大容量的600MW超临界循环流化床锅炉在神华国能集团四川白马循环流化床示范电站有限责任公司顺利通过168小时满负荷试运行成功投运。试运行期间,机组满负荷试运平均负荷率100.509%,保护装置投入率100%,热控自动投入率100%。这标志着我国在大容量、高参数循环流化床洁净煤燃烧技术方面走在了世界前列。
四川白马600MW超临界循环流化床示范电站是我国“十二五”重点工程,也是洁净煤炭燃烧这项高新技术应用的重大示范工程,更是我国首台乃至世界容量最大的超临界循环流化床示范电站工程。为全面提升国家重大技术装备自主创新能力,加快洁净煤技术推广应用,提高国家电力工业整体效率,充分利用有限资源,减少污染排放,建设资源节约型、环境友好型社会,东方电气集团东方锅炉股份有限公司在国家发改委、国家能源局、白马项目专家组的支持以及在白马电厂业主的全力配合下,2006年启动了国产600MW超临界循环流化床燃煤示范工程锅炉设计研制工作。2008年8月,国家发改委能源局正式下文批复:白马项目机组锅炉由东方锅炉牵头自主开发、自主设计、自主制造。2009年12月,技术方案顺利通过国家发改委专家组组织的评审。2011年该项目被列入国家重点新产品计划。2012年6月,世界首台最大容量600MW超临界循环流化床锅炉在东方锅炉制造完工。
世界首台600MW循环流化床示范机组锅炉的成功投运,对国家重大技术装备制造企业全面掌握600MW循环流化床原始设计技术,提高自主创新和自主开发能力,调整能源结构,实现能源发展与环境保护具有划时代的重大意义。
参考文献
[1]http://baike.baidu.com/view/1168352.htm
[2]吕俊复,张缦,杨海瑞,刘青,刘志强,赵勇纲. 简约型660MW超超临界循环流化床锅炉设计开发[J]. 中国电机工程学报,2014,05:741-747.
[3]吕俊复,于龙,张彦军,岳光溪,李振宇,吴玉新. 600MW超临界循环流化床锅炉[J]. 动力工程,2007,04:497-501+587. [4]刘静,王勤辉,骆仲泱,岑可法. 600MWe超临界循环流化床锅炉的设计研究[J]. 动力工程,2003,01:2179-2184+2204.