概述
超临界(SC)
火电厂超临界机组和超超临界机组指的是锅炉内工质的压力。锅炉内的工质都是水,水的临界压力是:22.115MP,临界温度是374.15℃ ;在这个压力和温度时,水和蒸汽的密度是相同的,就叫水的临界点,炉内工质压力低于这个压力就叫亚临界锅炉,大于这个压力就是超临界锅炉,炉内蒸汽温度不低于593℃或蒸汽压力不低于31 MPa被称为超超临界。目前,在工程上,也常常将25MPa以上的称为超超临界。
超临界、超超临界火电机组具有显著的节能和改善环境的效果,超超临.界机纲与超临界机纲.相比,热效率要提高1.2%,一年就可节约6000吨优质煤。未来火电建设将主要是发展高效率高参数的超临界(SC)和超超临界(USC)火电机组,它们在发达国家已得到广泛的研究和应用。
技术原理
1.理论基础
火力发电技术主要是由锅炉和汽轮机来完成的,为了节约能源,必须提高机组的发电效率。众所周知,从锅炉出来的蒸汽初参数对整个发电的效率有着直接影响(见图1)。由Rankine循环可知:提高汽压、汽温的主要目的是改善热循环效率。汽压与汽温不是能相互完全独立的两个变量,必须予以协调考虑,以做到排汽不过热,也不含湿过多,对再热机组都是有可能的。提高蒸汽参数的得益部分来自排汽量的减少,即排至凝汽器热量的减少。提高蒸汽压力还可增加抽气量,这样又进一步减少了排气量。
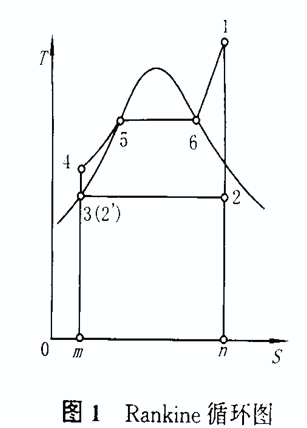
火力发电技术主要是由锅炉和汽轮机来完成的,为了节约能源,必须提高机组的发电效率。众所周知,从锅炉出来的蒸汽初参数对整个发电的效率有着直接影响(见图1)。由Rankine循环可知:提高汽压、汽温的主要目的是改善热循环效率。汽压与汽温不是能相互完全独立的两个变量,必须予以协调考虑,以做到排汽不过热,也不含湿过多,对再热机组都是有可能的。提高蒸汽参数的得益部分来自排汽量的减少,即排至凝汽器热量的减少。提高蒸汽压力还可增加抽气量,这样又进一步减少了排气量。
欲获取最大的热耗收益,汽温与汽压必须同步增加。以某一定汽压、汽温为基准,提高汽压,热耗随之减少,至一定程度后,热耗的减少量会逐渐缩小,此时,如能同时提高汽温,节能效果仍能有较显著的提高。蒸汽压力高则高压级的容积流量减少,泄漏损失及其他叶片损失相应增加。其他改善工况以降低热耗的措施,如增加再热次数、加热级数、提高给水温度及蒸汽温度等也都存在类似制约条件,也有优化间题。
由图1可知,1~2是蒸汽在汽轮机中绝热膨胀,并对外做功;2~3是膨胀终了的湿蒸汽在冷凝器中对冷却水定温定压放热并凝结成饱和水;3~4为凝结水在给水泵中被绝热压缩,压力升高,再次进入锅炉;4~1为高压水在锅炉中定压吸热,从未饱和水加热到过热蒸汽。
1.1蒸汽初温的影响
由图1可以看出,在初压p1和背压p2不变的情况下,提高初温可提高循环的平均吸热温度,从而提高循环的热效率。此外提高初温还可以增大乏汽的干度从而改善汽轮机的工作。但是初温的提高受到锅炉中过热器和汽轮机中叶片材料耐高温的限制,不能一味地追求高温。从理论上讲:当压力不变,主蒸汽和再热蒸汽温度从538℃提高到566℃时,汽轮机热耗约下降0.6%~0.7%。
1.2蒸汽初压的影响
在保持背压p2和初温T1不变而升高初压P1的情况下,提高p1可以提高平均吸热温度于 1,从而提高循环的热效率,然而提高初压会降低汽轮机排汽的干度,排汽中含水过多将会危及汽轮机的安全,并降低最后几级的工作效率。从理论上讲:当主蒸汽压力从16.5MPa提高到24.1MPa,汽轮机热耗约下降1.8%~2.0%。
总之,提高蒸汽初参数P1和T1,降低乏汽压力p2均可以提高循环效率。
由图1可知,1~2是蒸汽在汽轮机中绝热膨胀,并对外做功;2~3是膨胀终了的湿蒸汽在冷凝器中对冷却水定温定压放热并凝结成饱和水;3~4为凝结水在给水泵中被绝热压缩,压力升高,再次进入锅炉;4~1为高压水在锅炉中定压吸热,从未饱和水加热到过热蒸汽。
1.1蒸汽初温的影响
由图1可以看出,在初压p1和背压p2不变的情况下,提高初温可提高循环的平均吸热温度,从而提高循环的热效率。此外提高初温还可以增大乏汽的干度从而改善汽轮机的工作。但是初温的提高受到锅炉中过热器和汽轮机中叶片材料耐高温的限制,不能一味地追求高温。从理论上讲:当压力不变,主蒸汽和再热蒸汽温度从538℃提高到566℃时,汽轮机热耗约下降0.6%~0.7%。
1.2蒸汽初压的影响
在保持背压p2和初温T1不变而升高初压P1的情况下,提高p1可以提高平均吸热温度于 1,从而提高循环的热效率,然而提高初压会降低汽轮机排汽的干度,排汽中含水过多将会危及汽轮机的安全,并降低最后几级的工作效率。从理论上讲:当主蒸汽压力从16.5MPa提高到24.1MPa,汽轮机热耗约下降1.8%~2.0%。
总之,提高蒸汽初参数P1和T1,降低乏汽压力p2均可以提高循环效率。
2.超临界汽轮机发电的技术特点
火电机组蒸汽参数的提高和单机容量的增大是火电技术进步的重要标志。大型超临界汽轮机的应用,将明显降低热耗率,提高经济性,是当今世界动力工业的发展趋势之一。对于超临界火电机组技术经济指标主要有:
2.1可用率
国外在发展超临界技术初期,由于参数选择过高,超越了当时的冶金技术水平,因而投运后事故频繁,可靠性、可用率低。后来通过降低参数和改进技术,超临界机组可用率不断提高,目前已经达到亚临界机组的水平。日本的超临界机组可用率大多在99;我国石洞口二厂的2台进口超临界机组的可用率也达到了90%以上。
2.2机组效率和供电煤耗
根据朗肯循环原理,蒸汽参数越高热力循环的热效率就会越高。一般认为,24.1MPa/538℃/566℃的超临界机组可比16.7MPa/538℃/538℃亚临界机组的热效率高2.0%~2.5%,31MPa/566℃/566℃/566℃的超超临界机组热效率提高4%~6%。目前世界上运行的超临界机组的实际供电标准煤耗大体在310~329g/kWh,我国1998年火电机组的平均标准煤耗为404g/kWh,将要关停的3000万kW小火电机组标准煤耗更高达550g/kWh。如果其中的1/3容量用1000万kW超临界机组代替,每年可节约1100~1200万t标准煤,有十分可观的节能效果。
2.3调峰性能
国外超临界机组发展过程中,前期多为带基本负荷,随着核电的发展并承担了基本负荷,对大型火电机组的调峰性能越来越高,对机组提出变压运行的特殊要求,通过超临界机组的专有技术开发,现代超临界汽轮机有较好的热机动性,可采用复合变压运行方式,在低负荷下机组仍保持较高的效率,完全能够满足调峰需要。
2.4投资与收益
根据国内专家的估算,当把16. 7MPa/538℃/538℃的亚临界参数的机组提高为24.2MPa/538℃/566℃的超临界参数机组时,电站的比投资将增大2.0%左右,相应的供电效率可提高2.5%左右。需要有一定的年限将节省的煤价抵消投资的增量。因此煤价超过一定水平时,采用超临界机组是合适的。如果再考虑减少气体排放收费,可接受的煤价还可以低一些。因此,在煤价较高的地区使用超临界机组比较有利。
2.5环保效益
超临界机组煤耗低,与其他火电机组相比较,相同发电量下的SO2、NOx气体污染和温室效应气体CO2排放相对减少,有较好的环保效益。根据国家公开发表的统计数据,截至2003年末,我国火电机组装机容量已达285640MW,平均供电煤耗为378g/kWh,较国际先进水平高出10%以上。如果按2003年全国火力发电量15800亿kWh计算,全国一年多耗煤约6000万t,占全国煤炭生产原煤总量的3.6%(16.67亿t)。在燃煤电站使用超临界机组可提高煤炭利用率,实现节能降耗,降低环境污染,有利于环保。与16.7MPa/538℃/538℃的亚临界参数火电机组相比,采用538℃/566℃超临界机组可使CO2的排放量减少10%;采用600℃/620℃超超临界机组可使CO2的排放量减少15%;采用700℃/720℃超超临界机组可使CO2的排放量减少30%。再者现在的大型超临界机组大都装有脱硫脱硝装置以及除尘装置,所以对环境的污染就会更小。
火电机组蒸汽参数的提高和单机容量的增大是火电技术进步的重要标志。大型超临界汽轮机的应用,将明显降低热耗率,提高经济性,是当今世界动力工业的发展趋势之一。对于超临界火电机组技术经济指标主要有:
2.1可用率
国外在发展超临界技术初期,由于参数选择过高,超越了当时的冶金技术水平,因而投运后事故频繁,可靠性、可用率低。后来通过降低参数和改进技术,超临界机组可用率不断提高,目前已经达到亚临界机组的水平。日本的超临界机组可用率大多在99;我国石洞口二厂的2台进口超临界机组的可用率也达到了90%以上。
2.2机组效率和供电煤耗
根据朗肯循环原理,蒸汽参数越高热力循环的热效率就会越高。一般认为,24.1MPa/538℃/566℃的超临界机组可比16.7MPa/538℃/538℃亚临界机组的热效率高2.0%~2.5%,31MPa/566℃/566℃/566℃的超超临界机组热效率提高4%~6%。目前世界上运行的超临界机组的实际供电标准煤耗大体在310~329g/kWh,我国1998年火电机组的平均标准煤耗为404g/kWh,将要关停的3000万kW小火电机组标准煤耗更高达550g/kWh。如果其中的1/3容量用1000万kW超临界机组代替,每年可节约1100~1200万t标准煤,有十分可观的节能效果。
2.3调峰性能
国外超临界机组发展过程中,前期多为带基本负荷,随着核电的发展并承担了基本负荷,对大型火电机组的调峰性能越来越高,对机组提出变压运行的特殊要求,通过超临界机组的专有技术开发,现代超临界汽轮机有较好的热机动性,可采用复合变压运行方式,在低负荷下机组仍保持较高的效率,完全能够满足调峰需要。
2.4投资与收益
根据国内专家的估算,当把16. 7MPa/538℃/538℃的亚临界参数的机组提高为24.2MPa/538℃/566℃的超临界参数机组时,电站的比投资将增大2.0%左右,相应的供电效率可提高2.5%左右。需要有一定的年限将节省的煤价抵消投资的增量。因此煤价超过一定水平时,采用超临界机组是合适的。如果再考虑减少气体排放收费,可接受的煤价还可以低一些。因此,在煤价较高的地区使用超临界机组比较有利。
2.5环保效益
超临界机组煤耗低,与其他火电机组相比较,相同发电量下的SO2、NOx气体污染和温室效应气体CO2排放相对减少,有较好的环保效益。根据国家公开发表的统计数据,截至2003年末,我国火电机组装机容量已达285640MW,平均供电煤耗为378g/kWh,较国际先进水平高出10%以上。如果按2003年全国火力发电量15800亿kWh计算,全国一年多耗煤约6000万t,占全国煤炭生产原煤总量的3.6%(16.67亿t)。在燃煤电站使用超临界机组可提高煤炭利用率,实现节能降耗,降低环境污染,有利于环保。与16.7MPa/538℃/538℃的亚临界参数火电机组相比,采用538℃/566℃超临界机组可使CO2的排放量减少10%;采用600℃/620℃超超临界机组可使CO2的排放量减少15%;采用700℃/720℃超超临界机组可使CO2的排放量减少30%。再者现在的大型超临界机组大都装有脱硫脱硝装置以及除尘装置,所以对环境的污染就会更小。
国内发展和应用现状
煤炭在我国一次能源结构中具有资源优势,这决定了煤电在电源结构中的基础地位在一定时期内难以改变。据统计,截至2006年,全国火电装机已达4.84亿千瓦,占全国装机总容量的78%。发电用煤占煤炭产量的一半以上,火电装机的增长带动煤炭需求不断增长。
长期以来,我国燃煤发电存在煤耗高、环境污染严重和装机结构不合理等问题,并越来越受到煤炭供应、环境容量、交通运输能力等多重约束。要实现电力工业又好又快发展,就必须加快电源结构调整,研究开发污染排放少、发电效率高并可形成规模化应用的洁净煤发电技术。
超超临界燃煤发电技术正是我国迫切需要、符合我国国情的一种洁净煤发电技术。超超临界发电技术是在超临界燃煤发电技术的基础上,通过进一步提高主蒸汽的温度和(或)压力等级来不断提高发电效率,进而不断地提高燃煤发电机组的节能环保水平。因此,发展超超临界机组是我国发电业进行结构调整、实现又好又快发展的一个重要方向。
经过近半个世纪的发展,超临界和超超临界技术在美、日和欧洲部分工业化国家已进入成熟和商业化运行阶段,这为我国利用国外已开发的技术成果、发挥后发优势、实现跨越式发展提供了机会。
与此同时,与其他新型发电技术相比,超超临界发电技术具有技术继承性,技术难点也较少,最有条件在短时间内实现规模化生产。我国基本具备了发展超超临界技术的基础条件:30万千瓦、60万千瓦亚临界机组装备制造水平已与世界先进水平接近;中国华能集团引进建设60万千瓦超临界机组,以及建设沁北电厂首台国产60万千瓦超临界机组,为开发更高等级燃煤发电技术积累了设计和运行经验。
综合上述优势,从现实国情和现有技术条件出发,我国做出了发展国产超超临界机组的决策,并决定以华能玉环电厂为依托工程,由中国华能集团公司负责牵头实施,以产学研联合体的方式,共同开发具有我国自主知识产权的超超临界发电技术。2002年8月,国家863计划“超超临界燃煤发电技术”正式立项。2004年6月,华能玉环电厂正式开工。同年11月24日,华能沁北电厂传来首台国产60万千瓦超临界机组投产的捷报。2006年12月30日,华能玉环电厂首台百万千瓦超超临界机组投产。
国外发展和应用现状
目前,美国投运的超临界机组大约为170台,其中燃煤机组占70%以上。前苏联300MW及以上容量机组全部采用超临界参数。至1988年已有近200台超临界机组投入运行,全国35%电力由超临界机组供给。
日本的超临界机组共有100多台,总容量为超过5760万千瓦,占火电机组容量的61%,45万千瓦及以上的机组全部采用超临界参数,而且在提高参数方面做了很多工作,最高压力为31MPa,最高温度已达到600/600°C。
丹麦史密斯公司研究开发的前2台超超临界机组,容量为400MW,过热蒸汽出口压力为29MPa,二次中间再热、过热蒸汽和再热汽温为582/580/580℃,机组效率为47%,机组净效率达45%(采用海水冷却,汽轮机的背压为26kPa);后开发了参数为30.5MPa,582/600℃、容量为400MW的超超临界机组,该机组采用一次中间再热,机组设计效率为49%。
德国西门子公司20世纪末设计的超超临界机组,容量在400~1000MW范围内,蒸汽参数为27.5MPa, 589/600℃,机组净效率在45%以上。
欧洲正在执行“先进煤粉电厂(700℃)”的计划,即在未来的15年内开发出蒸汽温度高达700℃的超超临界机组,主要目标有两个: 使煤粉电厂净效率由47%提高到55%(采用低温海水冷却)或52%(对内陆地区和冷却塔);降低燃煤电厂的投资价格。美国和日本也将蒸汽温度为700℃的超超临界机组作为进一步的发展目标。
供应商信息
德国西门子公司
丹麦史密斯公司
中国华能集团公司
三菱公司(MHI)
经典案例
绥中发电厂800WM超临界燃煤锅炉技术经验总结分析
摘要:本文针对绥中电厂锅炉设备在近几年运行中出现的问题分析,阐述了我公司工程技术人员对俄罗斯生产的800WM超临界燃煤锅炉从认识、掌握、改造、驾驭的全过程,为我国电力工业吸收掌握进口大机组提供了经验。
1 锅炉设备概况
绥中发电有限责任公司一期工程是由俄罗斯塔干罗格锅炉厂生产的ПП-2650-25-545KT超临界中间再热直流锅炉,其结构特点为单炉膛、全悬吊、“T”型布置及全气密式密封鳍片水冷壁结构。两对流竖井外侧墙中心线距离48340mm,前后墙中心线距离30986mm,顶棚水冷壁标高81000mm,炉顶板梁上部标高97800mm。
每台锅炉分两个流道,其水冷壁为多次串联垂直上升式,分上、下辐射区,从而构成水冷壁的四个流程,水冷壁管是Φ32×6×46mm的12Cr1MoV合金管构成,在炉膛上部出口部分顺着烟气流动方向依次布置鳃管、屏式过热器Ⅰ、Ⅱ、Ⅲ,费斯顿管Ⅰ、对流过热器、费斯顿管Ⅱ,高温再热器,费斯顿管Ⅲ,在对流竖井内依次布置是:480根省煤器辅助悬吊管,低温再热器,省煤器。
绥中发电有限责任公司一期工程是由俄罗斯塔干罗格锅炉厂生产的ПП-2650-25-545KT超临界中间再热直流锅炉,其结构特点为单炉膛、全悬吊、“T”型布置及全气密式密封鳍片水冷壁结构。两对流竖井外侧墙中心线距离48340mm,前后墙中心线距离30986mm,顶棚水冷壁标高81000mm,炉顶板梁上部标高97800mm。
每台锅炉分两个流道,其水冷壁为多次串联垂直上升式,分上、下辐射区,从而构成水冷壁的四个流程,水冷壁管是Φ32×6×46mm的12Cr1MoV合金管构成,在炉膛上部出口部分顺着烟气流动方向依次布置鳃管、屏式过热器Ⅰ、Ⅱ、Ⅲ,费斯顿管Ⅰ、对流过热器、费斯顿管Ⅱ,高温再热器,费斯顿管Ⅲ,在对流竖井内依次布置是:480根省煤器辅助悬吊管,低温再热器,省煤器。
额定蒸发量:2650t/h; 再热蒸汽流量:2151.5t/h
主蒸汽温度: 545℃; 主蒸汽压力: 25.01MPa
再热器入口压力:3.86MPa; 再热器入口温度: 283℃
再热器出口压力:3.62MPa; 再热器出口温度: 545℃
给水温度:277℃; 排烟温度:134℃
热风温度:320℃;
2 设备试运中存在主要问题分析
2.1 燃烧器烧损
2.1 燃烧器烧损
锅炉吹管结束后遇到的第一个主要问题就是燃烧器烧损。因燃烧器烧损问题共延误启机约40天。1999年12月14日18:03因#6喷燃器着火锅炉停炉。对#6喷燃器隔离后机组再次启动,1999年12月16日16:39因发电机失磁保护动作停机。停机后检查发现除#6喷燃器外,#27、33喷燃器一次风蜗壳烧损,另外大部分喷燃器喷口变形,旋流片烧损。通过分析检查,燃烧器烧损的主要原因如下:a.俄规程规定在70%负荷以上时启动烟气再循环风机,在烟气再循环风机停运时由于烟气回流且烟风挡板不严造成火焰回流烧损喷燃器。b.油枪根部配风不足,导致火焰延伸不到炉膛内。主要采取的措施是:a.点火时即启动烟气再循环风机,保证烟气再循环风机出口为正压,防止烟气经再循环烟道回流。b.任何时候均保证各喷燃器中心风压大于0.4KPa。c.油枪点火时通入一次风以补充中心风的不足。d.燃烧器蜗壳加装壁温测点,运行中加强监视。
2000年3月7日因#39喷燃器着火锅炉停炉。本次喷燃器烧损的直接原因为二级煤粉分配挡板运行中改变了位置,导致#39喷燃器供入一次风量下降。针对燃烧器烧损现象,首先我们对所有二级分配器进行了检查,并重新进行了一次风调平工作。为防止分配挡板移位,采用焊接的方法将其固定,其次通过管道阻力计算重新确定了磨煤机运行中风量不低于8.5×104Nm3/h,一次风速由16~18m/s全部提至18m/s以上。通过运行观察及利用停用时间抽查,燃烧器运行正常。
2.2 锅炉费1管爆破
燃烧器烧损问题解决后锅炉遇到的主要问题就是锅炉费1管爆破。费1管的作用是悬吊锅炉两侧墙水冷壁,其管径较粗(Ф89×14)。#1炉在2000年3月30日、4月20日、5月9日共发生三次费1管爆破事故。因锅炉费1管爆破共延误启机时间约2个月。经过分析中方人员认为费1管爆破的主要原因是锅炉设计缺陷,即在多根并列费1管间流量不均,而费1管流速低、所处烟温高,管内工质又处在大比热区,由于流量不均造成部分管子超温最终爆管。刚开始专家不承认费1管爆破是锅炉设计原因,俄方曾提出将锅炉点火流量增加到40%额定流量并进行给水流量扰动试验,但我方认为从几次爆管情况看即使锅炉点火流量增加到40%额定流量仍有可能出现费1超温现象,而且锅炉点火流量增加将增加很多启动损失。按俄专家建议在费1管炉内及炉外加装壁温测点,而且割除两侧中间。
3 生产阶段设备存在主要问题分析
锅炉设备从1999年投产以来,四管曾多次发生漏泄,严重影响机组的长期安全稳定运行,绥电公司的工程技术人员同有关专家一起针对发现的问题科学地分析,积极的探索解决方案并逐步实施,先后解决了“四管”漏泄的诸多问题,为保证机组的长期安全稳定运行打下良好的基础,具体表现如下四个方面:
锅炉设备从1999年投产以来,四管曾多次发生漏泄,严重影响机组的长期安全稳定运行,绥电公司的工程技术人员同有关专家一起针对发现的问题科学地分析,积极的探索解决方案并逐步实施,先后解决了“四管”漏泄的诸多问题,为保证机组的长期安全稳定运行打下良好的基础,具体表现如下四个方面:
3.1 锅炉水冷壁四角漏泄
绥中电厂一期两台800MW超临界机组锅炉炉膛四角水冷壁自投产以来先后共发生9次漏泄,经分析其原因:是由于原俄罗斯设计的炉膛四角附加鳍片过宽,在运行时鳍片中部得不道充分冷却,致使角部鳍片热应力过大,致使鳍片在搭接应力集中点处产生横向裂纹,然后裂纹逐渐发展至水冷壁母材,最终导致锅炉四角水冷壁的漏泄。现在通过绥中电厂有关专业人员共同分析研究并制定了锅炉四角改造方案:方案主要采用美国程序ANSYS对我厂原角部水冷壁结构以及改造后结构进行温度场比较分析。此计算模型建立在下列基础上:(1)水冷壁角部尺寸有现绥电#1锅炉实际尺寸与改进后尺寸;(2)炉膛烟气温度都取1000℃,与水冷壁表面进行热交换;(3)水冷壁背火面都按绝热边界条件处理;(4)水冷壁内部介质温度取410℃设定。通过计算模型比较两种不同结构在相同的环境中,温度分布存在明显差异:俄罗斯设计的构造温度场不合理,角部鳍片中部因无介质冷却,比正常的水冷壁管高出近120℃,并且长期作用。改进后的角部水冷壁为切角管屏布置,改进后的角部两根水冷壁按切角(近45℃)相连,管间距明显降低(原设计管间鳍片尺寸为14mm,改进后为10.5mm),由于改进后减少了管屏间鳍片的宽度,改善了鳍片的冷却效果,大幅度的减少了热偏差,温度场显示结果发现:改后的鳍片温度与其他区域的鳍片温度分布相同,基本不存在热偏差,改进后的构造降低了热应力(见附图1)。此方案在2004年#1机组大修中实施,预测改造后能够彻底地消除水冷壁四角漏泄,保证机组的稳定运行,减少机组的非停次数。
绥中电厂一期两台800MW超临界机组锅炉炉膛四角水冷壁自投产以来先后共发生9次漏泄,经分析其原因:是由于原俄罗斯设计的炉膛四角附加鳍片过宽,在运行时鳍片中部得不道充分冷却,致使角部鳍片热应力过大,致使鳍片在搭接应力集中点处产生横向裂纹,然后裂纹逐渐发展至水冷壁母材,最终导致锅炉四角水冷壁的漏泄。现在通过绥中电厂有关专业人员共同分析研究并制定了锅炉四角改造方案:方案主要采用美国程序ANSYS对我厂原角部水冷壁结构以及改造后结构进行温度场比较分析。此计算模型建立在下列基础上:(1)水冷壁角部尺寸有现绥电#1锅炉实际尺寸与改进后尺寸;(2)炉膛烟气温度都取1000℃,与水冷壁表面进行热交换;(3)水冷壁背火面都按绝热边界条件处理;(4)水冷壁内部介质温度取410℃设定。通过计算模型比较两种不同结构在相同的环境中,温度分布存在明显差异:俄罗斯设计的构造温度场不合理,角部鳍片中部因无介质冷却,比正常的水冷壁管高出近120℃,并且长期作用。改进后的角部水冷壁为切角管屏布置,改进后的角部两根水冷壁按切角(近45℃)相连,管间距明显降低(原设计管间鳍片尺寸为14mm,改进后为10.5mm),由于改进后减少了管屏间鳍片的宽度,改善了鳍片的冷却效果,大幅度的减少了热偏差,温度场显示结果发现:改后的鳍片温度与其他区域的鳍片温度分布相同,基本不存在热偏差,改进后的构造降低了热应力(见附图1)。此方案在2004年#1机组大修中实施,预测改造后能够彻底地消除水冷壁四角漏泄,保证机组的稳定运行,减少机组的非停次数。
3.2 锅炉再热器事故喷水出口管道裂纹
由于我公司两台直流锅炉在设计上存在再热器系统肥大的缺陷,自机组试运至今,运行中冷段再热器出口蒸气温度经常超过报警值(485℃),热段再热蒸汽出口温度一直依靠事故减温水的投入才能维持额定。通过我厂近两年来的实际运行经验表明:再热器事故减温水的大量投入,不仅降低了机组的循环热效率,而且由于减温器在长期受冷热交变应力的影响下,减温器的出口汇合联箱管道多次产生疲劳裂纹,严重的威胁锅炉的稳定运行。为了解决此问题,绥中电厂相关技术人员制定了再热器系统改造方案:在每1/4流道的8根汽-汽交换器的二次汽入口管的4根加装节流孔板(孔板直径ф15mm),在一定程度上减少了流经汽-汽交换器的二次蒸汽流量。通过汽交系统的改造:改造后的系统参数在相同负荷的条件下,排除其他因素的影响,汽-汽交换器出口即冷段再热器入口温度较改造前平均下降5-10℃,而冷段再热器出口温度变化不大,事故减温水流量相对降低了。
3.4 锅炉省煤器联箱管座角焊缝进行磁记忆检查
锅炉“四管”漏泄其中省煤器漏泄占很大比重,严重的威胁锅炉的安全稳定运行,绥中电厂省煤器联箱角焊缝也存在原始缺陷,在运行过程中曾多次发生漏泄。为了解决此问题,绥中电厂对省煤器角焊缝主要采用了金属磁记忆检查的方法,检验工作主要采用俄罗斯“动力诊断”公司研制的“金属材料应力集中测试仪”,通过检验确定母材及焊缝中的应力集中区,然后采用裂纹指示仪对母材及焊缝应力集中区表面进行进一步的检验。通过2002年、2003年先后两次对#2炉16个省煤器上联箱上的管座2256道角焊缝进行了检查,共发现11个管座角焊缝存在严重的应力集中,并对此11个角焊缝进行了挖补处理并经超声检验合格。通过对原始缺陷的处理,避免了省煤器因角焊缝缺陷导致省煤器漏泄的发生。自省煤器角焊缝缺陷处理后,绥电一期工程两台炉未发生一次省煤器角焊缝漏泄情况。通过对省煤器角焊缝进行磁记忆检查有力的制止了省煤器漏泄的问题。
4 锅炉运行调节技术
通过三、四年的探索,绥电运行人员在对超临界机组的驾驭水平上正不断提高,也总结出一套行之有效的启停和运行调节手段。
4 锅炉运行调节技术
通过三、四年的探索,绥电运行人员在对超临界机组的驾驭水平上正不断提高,也总结出一套行之有效的启停和运行调节手段。
锅炉采用全压启动,在锅炉点火前即建立启动压力,保持内置闸阀前压力为25MPa的额定值。同时,为保证锅炉水冷壁良好的水动力工况,要求机组在建立启动压力的同时,必须同时建立起启动流量;根据直流锅炉的设计要求,此流量不得低于锅炉额定蒸发量30%,即保证锅炉单流道给水流量在400T/h以上的范围内。
按锅炉厂提供的规程规定,锅炉在机组负荷达到360MW后,开始进行转直流操作。通过实际操作发现,其分进阀的通流能力较设计水平低,在锅炉燃烧率和给水量达到360MW的水平时,分进阀的通流量明显不足,表现为内置闸阀前温度、压力急剧升高。特别是对温度比较敏感的鳃管区域的温度,常常会导致其金属温度超限。根据这种情况,通过观察参数变化趋势,总结出在机组负荷控制在280~320MW的水平进行转直流操作比较稳定。此时,锅炉内置闸阀前的各项参数基本上接近于额定参数,锅炉燃料量变化扰动对汽温、汽压的影响相对较弱,加之启动减温水有一定的开度,可防止锅炉直流工况下,通流量增加导致汽温降低。
给水调节可通过改变单流道给水流量进行单独调节,也可以通过改变总给水流量最后作用在两个流道而完成共同调节,锅炉蒸汽温度的调节通过调节每个流道的减温水定值进行单独调节,两个流道介质之间没有相互联系。锅炉燃烧调节采用全炉膛调节方式,通过控制进入喷燃器的二次风量来改变煤粉混合的强烈程度,从而调整火焰中心位置,最终达到调节两侧温度偏差的目的。
锅炉设计燃用晋北烟煤,后改烧神华煤,由于神华煤的易结焦性,在锅炉的实际运行中,经常出现锅炉吹灰过程中掉焦将渣沟堵塞的现象。通过实际运行观察,采用混煤的燃烧方式能够极大程度改善灰渣的结焦特性,特别是采用炉前混煤的方式,效果更好。通过运行技术人员的不懈努力和探索,目前,单机日发1868万千瓦时,双机日发3600万千瓦时,锅炉完全可以在100%负荷下连续运行。
此外,合理运用锅炉设计过程中一些措施以及燃料性质来改善煤粉的燃烧特性也能在很大程度上控制结焦,我公司锅炉较设计高度加高了6米,利用神华煤挥发份高,燃烬性能好的特点,我们降低旋流喷燃器的旋流强度,同时增加煤粉细度,来延长煤粉的燃烧时间,使锅炉水冷壁区域的容积热负荷和壁面热负荷得到有效降低,NOx的排放浓度降至226mg/Nm3低于国家控制标准,同时由于炉膛较高,也不致引起水平烟道的结焦加剧和飞灰热损失的增加。
5 机组现在运行状态及生产指标
2003年全年,我公司#1机组实现连续运行157天,跨年度连续运行173天;#2机组实现连续运行153天,双机实现连续运行88天。锅炉效率完成92.35%,排烟温度完成132℃,飞灰可燃物完成0.46%。均优于设计值。
2003年全年,我公司#1机组实现连续运行157天,跨年度连续运行173天;#2机组实现连续运行153天,双机实现连续运行88天。锅炉效率完成92.35%,排烟温度完成132℃,飞灰可燃物完成0.46%。均优于设计值。
6 结束语
绥中电厂属于我国原来引进单机容量最大机组,同时这台机组也是俄罗斯生产的第一台引进燃煤机组,设计经验不完全成熟,机组原始设计缺陷很多,同时也没有同类机组运行检修经验借鉴,但从设备安装投产到现在,我公司专业技术人员从摸索、掌握、改造、驾驭设备基础上,大胆挖掘创新,使机组运行指标超过设计值,居全国之首,也完全优于俄罗斯现在运行的同类机组水平。我们技术人员始终本着不断创新、持续发展的原则,立足本职工作,为中国电力事业乃至世界科学的发展做出我们最大的贡献。
绥中电厂属于我国原来引进单机容量最大机组,同时这台机组也是俄罗斯生产的第一台引进燃煤机组,设计经验不完全成熟,机组原始设计缺陷很多,同时也没有同类机组运行检修经验借鉴,但从设备安装投产到现在,我公司专业技术人员从摸索、掌握、改造、驾驭设备基础上,大胆挖掘创新,使机组运行指标超过设计值,居全国之首,也完全优于俄罗斯现在运行的同类机组水平。我们技术人员始终本着不断创新、持续发展的原则,立足本职工作,为中国电力事业乃至世界科学的发展做出我们最大的贡献。
参考文献
[1]研发超超临界燃煤发电技术走持续发展之路.