0 引言
为了全面实施燃煤电厂超低排放和节能改造,2015年,国家环保部印发《全面实施燃煤电厂超低排放和节能改造工作方案》,加快现役燃煤发电机组超低排放改造步伐,即在基准氧含量6%条件下,烟尘、SO2、氮氧化物排放浓度分别不高于10、35、50 mg/m3。许多燃煤发电企业、高校及科研院所已经开始了深度脱硫技术(综合脱硫效率不小于98%,且SO2实现超低排放)的研究。
循环流化床燃烧技术是20世纪70年代末发展起来的清洁煤燃烧技术。在800~900℃下,燃烧稳定。加入一定粒径的石灰石颗粒,石灰石中的碳酸钙分解成高孔隙率的氧化钙,进而吸收燃料燃烧生成的SO2。在此温度范围,氮氧化物的生成量较低。另外,煤种适应性强,尤其是燃用煤矸石、煤泥等低热值燃料利于煤炭资源的综合利用。因此,近20年,CFB(循环流化床)锅炉技术在我国得到迅速发展,循环流化床锅炉机组发电容量近1亿kW,总循环流化床锅炉台数大于3000台,其工程应用已发展到600MW超临界等级。通过炉内喷入石灰石粉实现高效脱硫是CFB锅炉的特点,也是CFB锅炉得以迅速发展的主要原因之一。由于炉内干法脱硫技术具有工艺流程简单、初投资及运行费用较低等优点,CFB锅炉设计阶段大多配置有炉内干法脱硫装置。一般认为,CFB锅炉在加入石灰石量达到Ca/S约为2.5时,可以实现90%以上的脱硫效率。对于相当大一部分折算硫分较高的CFB锅炉机组,单纯依靠炉内干法脱硫装置实现SO2超低排放并长周期稳定运行存在较大难度。
因此,本文结合试验台试烧试验研究结果和工程应用实例研究了CFB锅炉机组深度脱硫技术,并提出了实现SO2超低排放的技术策略。
1 CFB锅炉SO2的生成量
在实际运行中,CFB锅炉SO2的实际生成量一般会低于以全硫计算的理论排放量,CFB锅炉SO2的实际生成量主要取决于以下几个因素。
1.1 煤的硫分中可燃硫所占比例
煤中硫分按其在空气中能否燃烧可分为可燃硫和不可燃硫。可燃硫在CFB锅炉燃烧过程中的主要产物是SO2,包括有机硫、硫铁矿硫和单质硫,都能在空气中燃烧,占煤中硫分的90%以上;不可燃硫不能在空气中燃烧,在一定的温度区间也不发生分解,可看作是惰性的,主要以硫酸钙的形式存在。硫分中可燃硫所占的比例大则燃烧过程中SO2的实际排放值高,反之亦然。
1.2 煤灰中CaO 等碱金属氧化物含量
煤灰中含有CaO、MgO和Fe2O3等碱金属氧化物,其会与烟气中的SO2反应生成碱金属的硫化物,煤灰中还有诸多多孔介质类物质,对SO2有一定的固定作用,在定性分析时,常采用燃料自身钙硫物质的量比来间接判断SO2的实际排放值。自身钙硫物质的量比Ks,self定义为:
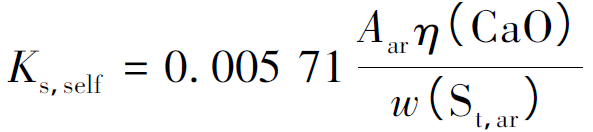
式中,Ks,self为燃料自身钙硫物质的量比;Aar为燃料灰分,%;η(CaO)为煤灰中氧化钙含量,%;w(St,ar)为煤的收到基硫分,%。
1.3 锅炉运行参数
锅炉运行参数中床温和氧含量对于SO2的实际排放影响最大。在运行床温低于850℃时,随着床温的升高,煤灰中碱金属的固硫反应速度呈增长趋势。床温高于850℃时,随床温的进一步提高,固硫反应速度开始下降,另外,已经生成的碱金属硫化物还会逆相分解生成SO2,煤中以硫酸钙形式存在的不可燃硫也会发生分解反应生成SO2。
固硫反应阶段需要氧气的参与,当锅炉运行氧含量过低时会限制固硫反应的进行。另外,当O2的分压过小时,CaSO4不稳定,将会发生还原反应:
CaSO4 + CO →CaO + SO2 + CO2 (1)
实际运行中,兼顾煤的燃尽程度,CFB锅炉过量空气系数不宜低于1.1,即炉膛出口氧含量不低于2%。对于挥发分低的难燃煤种,过量空气系数需进一步提高。
2 CFB锅炉脱硫工艺
CFB锅炉常采用的脱硫工艺包括炉内干法脱硫,CFB-FGB半干法脱硫和石灰石-石膏湿法脱硫。
2.1 炉内干法脱硫
CFB锅炉通过向炉内直接添加石灰石来控制SO2排放,在流化床燃烧温度下(800~900℃),投入炉内的石灰石首先在高温条件下煅烧发生分解反应生成氧化钙,然后氧化钙、SO2和氧气经过化学反应生成硫酸钙,化学反应方程式为:
CaCO3 →CaO + CO2 (2)
CaO + SO2 + 0.5 O2 →CaSO4 (3)
生成的固体硫酸钙随炉渣、飞灰一起排出炉膛,达到固硫的目的。
2.2 CFB-FGB 半干法脱硫
从锅炉的空气预热器出来的烟气进入循环流化床脱硫塔,通过喷水降温,使烟温降至高于烟气绝热饱和温度15℃左右,烟气中的SO2与加入的水、吸收剂、循环脱硫灰充分混合,进行脱硫反应,生成的脱硫副产物CaSO3·1/2 H2O 随飞灰排出。
2.3 石灰石-石膏湿法脱硫
石灰石-石膏湿法脱硫工艺通常以石灰石为脱硫吸收剂,通过向吸收塔内喷入吸收剂浆液,使之与烟气充分接触、混合,对烟气进行洗涤,烟气中的SO2与浆液中的碳酸钙以及鼓入的强制氧化空气发生化学反应,生成CaSO4·2H2O,达到脱除SO2的目的。
2.4 常用脱硫工艺的比较
表1对3种不同的脱硫工艺进行技术比较。炉内干法脱硫是目前CFB锅炉应用最广泛的一种脱硫工艺,我国白马600MW CFB发电机组上也采用的是该脱硫工艺系统。随着该工艺研究的深化,炉内干法脱硫工艺的脱硫效率不断提升,当Ca/S在2.0~3.0,大部分CFB锅炉脱硫效率可达到90%~95%。该工艺的投资及运行成本是3种脱硫工艺中最低的。
表1 脱硫工艺比较
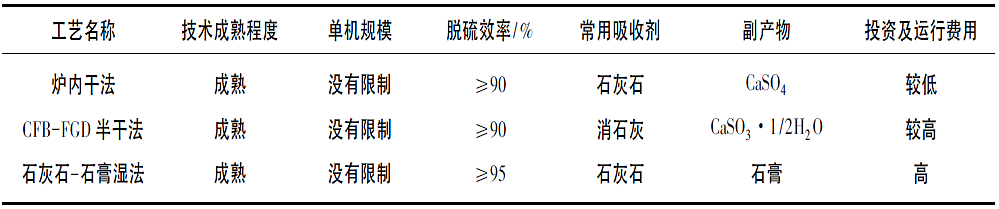
CFB-FGD半干法脱硫工艺,脱硫效率达到90%以上,可实现脱硫除尘一体化,同时满足SO2和烟尘的排放要求,我国300MW等级CFB发电机组上具有应用业绩,投资及运行成本低于石灰石-石膏湿法脱硫工艺。
石灰石-石膏湿法脱硫工艺平均脱硫效率最高,一般可达95%以上,投资及运行成本最高,脱硫产物石膏具有进一步利用的潜力。
3 CFB 锅炉深度脱硫技术
当CFB锅炉机组需达到98%以上的综合脱硫效率才能满足SO2超低排放的要求时,单一脱硫工艺很难保证SO2的长周期、稳定达标排放。分析认为通过降低锅炉SO2的生成量,采用炉内干法和烟气脱硫工艺联合脱硫的方式可实现深度脱硫的目标,并具有更高的调节灵活性和运行可靠性。
3.1 SO2生成量的降低
SO2的实际生成量与煤种和锅炉运行参数等因素有关,而要通过改变燃用煤种来降低燃煤的硫分存在较大的困难。因此,对于燃用煤种稳定的CFB锅炉,通过优化锅炉运行参数降低SO2的生成量是最可行的。
锅炉运行参数中床温是影响SO2的实际排放浓度的首要因素。虽然大部分CFB锅炉设计床温在800~900℃,但实际运行中普遍存在运行床温过高的问题,主要原因有以下几方面:①锅炉在设计过程中存在受热面布置不合理、分离器效率低等设备问题;②锅炉实际燃用煤种与设计煤种差别较大,造成灰分偏低、热值偏高等;③锅炉运行中为提高锅炉燃烧效率,降低锅炉不完全燃烧热损失而人为提高运行床温。
中国华能集团清洁能源技术研究院有限公司在1MW CFB试验台进行了不同区域的煤种试烧试验,研究不同煤种SO2生成量随床温的变化趋势,部分试验结果如图1所示。试验结果表明:随着床温的升高,SO2的生成量逐渐提高,自脱硫效率逐渐降低。因此,将锅炉运行床温尽可能控制在合理范围是降低SO2生成量的必要条件。
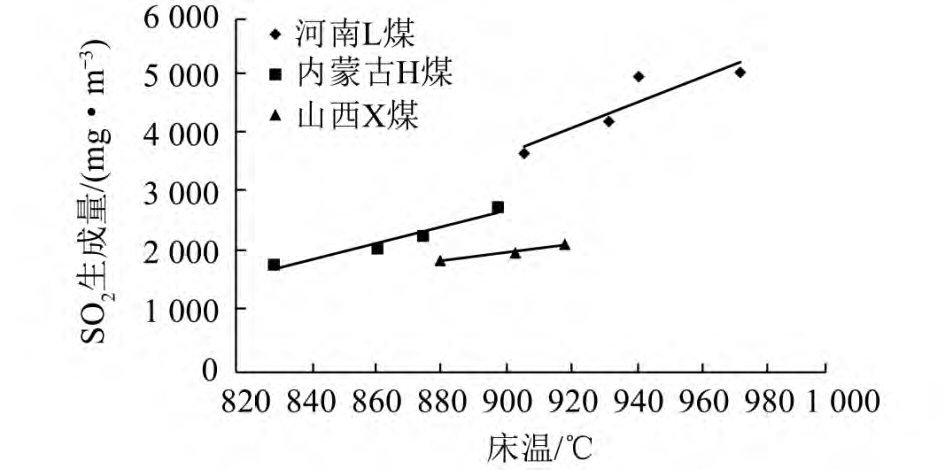
图1 SO2生成量随床温变化趋势
3.2 炉内高效脱硫
典型的CFB锅炉炉内高效脱硫工程实例见表2。由表2可见,3台典型CFB锅炉SO2理论生成量较高,炉内综合脱硫效率均达到了97%以上,实现了炉内高效脱硫。国内外大量试验研究及实炉运行结果均表明,将影响炉内干法脱硫效率的各种因素控制在合理的范围内,能够实现综合脱硫效率不低于95%(含自脱硫)的炉内高效脱硫。
3.2.1 石灰石物化参数
脱硫剂石灰石影响炉内脱硫效率的主要参数包括石灰石的脱硫反应活性、粒径分布和氧化钙含量。
表2 典型CFB锅炉炉内高效脱硫效果(含自脱硫)
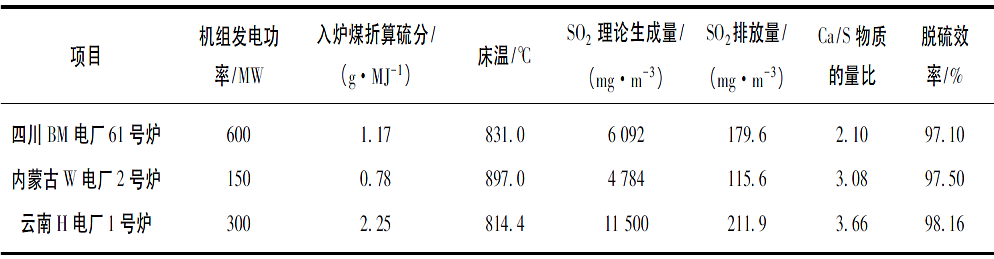
石灰石的脱硫反应活性可表述为石灰石与SO2进行表面化学反应的难易程度,受到石灰石成分和内部微观结构等因素的影响。不同产地的石灰石存在较大的差别,通常通过实验室热重试验进行评价。
石灰石颗粒的粒径分布要保证大部分颗粒能够被锅炉的旋风分离器分离而多次利用。锅炉设备生产厂家根据设计的分离器效率推荐石灰石的粒径分布,一般情况下石灰石中位粒径d50(粒径分布的筛分曲线上,筛上物的累积筛余量或通过量为50%的颗粒所对应的粒径) 为250~450μm,最大粒径dmax,为1.0~1.5mm。工程应用中可以结合飞灰和循环灰粒径分布综合考虑。
氧化钙含量用于评价石灰石的纯度,相同条件下优先选取氧化钙含量高的石灰石作为脱硫剂。
3.2.2 炉内干法脱硫系统参数
炉内干法脱硫工艺系统设计参数包括石灰石输送量、输送风速、输送物料浓度等。
炉内干法脱硫系统虽然属于气力输送的范畴,但由于石灰石粉堆积密度大、逸气性强、磨损指数大,易沉积板结的特性,在工艺系统设计上和其他粉粒体气力输送较大的差异。因此,炉内干法脱硫工艺系统核心参数选取和自动控制策略的制定都需要根据石灰石、煤种和锅炉炉型等因素综合考虑方可达到理想的效果。
3.2.3 锅炉运行参数
在工程应用中,可通过锅炉运行参数的调整试验和锅炉设备的改造,优化锅炉的运行床温和运行氧含量。部分现役CFB 锅炉机组通过锅炉受热面、高温旋风分离器、布风装置等锅炉主循环回路设备改造,优化锅炉运行参数,提高脱硫效率取得了一定的效果。
内蒙古W电厂2台CFB锅炉设计运行床温885 ℃,由于设计过程中受热面布置不合理,造成2台锅炉在满负荷时平均运行床温达到938 ℃以上。锅炉运行中存在脱硫用石灰石耗量大、SO2排放不稳定等问题。2014年2号炉通过炉膛受热面技术改造,满负荷时运行床温降至897℃,改造后SO2排放稳定。据统计,2014年7月在满足SO2排放值不高于200 mg/m3的条件下,2号炉日平均石灰石用量266t,而1号炉日平均石灰石用量511t。
提高炉内干法脱硫效率不应以大幅度牺牲钙硫比为代价,根据工程经验钙硫比的选取最大不宜高于4.0,且石灰石粉与入炉煤质量比不宜高于1:5。石灰石粉的大比例加入会造成CFB锅炉脱硫热损失增加、受热面磨损加剧、NOx生成量升高等负面影响。
3.3 CFB 锅炉烟气脱硫工艺选择
烟气脱硫工艺的选取需要综合考虑脱硫设施的建设场地,脱硫剂的来源、成本,脱硫系统的建设及运行成本和脱硫副产品的销路等因素。
石灰石-石膏湿法脱硫是燃煤机组常用的烟气脱硫工艺。该工艺需要进行脱硫塔和烟囱的防腐,由于我国天然石膏矿产丰富、脱硫石膏含水率较高等原因,副产品石膏销售困难。
由于大部分CFB锅炉均配备有炉内干法脱硫系统,炉内脱硫后的飞灰中CaO含量较高,在10%以上。采用CFB-FGD半干法脱硫工艺可以充分利用飞灰中CaO,降低脱硫系统的运行成本。另外该工艺不需要进行脱硫塔和烟囱的防腐,因此系统的建设成本低于湿法脱硫工艺。以某300MW CFB锅炉为例,设计入口SO2浓度为1500mg/m3,实现SO2超低排放,半干法与湿法2种工艺的投资与生产成本对比如图2所示。
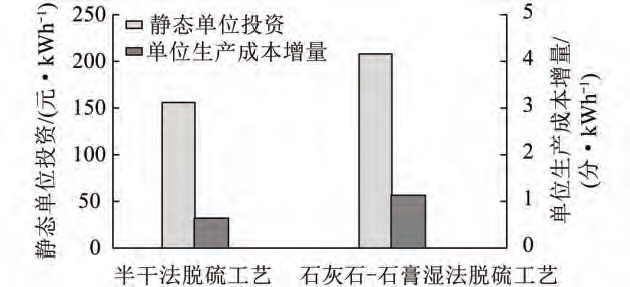
图2 300MW CFB锅炉烟气脱硫工艺经济指标对比
图2中石灰石-石膏湿法脱硫工艺投资含烟囱防腐投资。不同区域由于标杆电价和脱硫剂成本等因素的差异,会有所区别。神华(福建)能源有限责任公司所辖YS电厂2×300MW CFB锅炉是国内最早开展污染物超低排放改造的300MW级CFB锅炉机组之一。通过技术经济性分析,采用炉内干法脱硫+烟气CFB-FGD半干法脱硫除尘一体化工艺进行SO2和烟尘脱除,采用SNCR( 选择性非催化还原)高效脱硝工艺进行NOx脱除,2015年改造完成后,实现了SO2、NOx和烟尘的超低排放。
SO2超低排放技术路线保留了原炉内干法脱硫系统,设计通过炉内干法脱硫将锅炉尾部受热面出口(脱硫塔入口)SO2浓度控制在1500mg/m3以下,烟气半干法脱硫系统进一步脱除,将烟气中的SO2控制在35mg/m3以下。烟气半干法脱硫系统2015年11月17日通过了168h连续试运行。
炉内干法脱硫+烟气CFB-FGD半干法脱硫两级脱硫系统主要技术参数见表3和表4。
表3 炉内干法脱硫系统主要参数
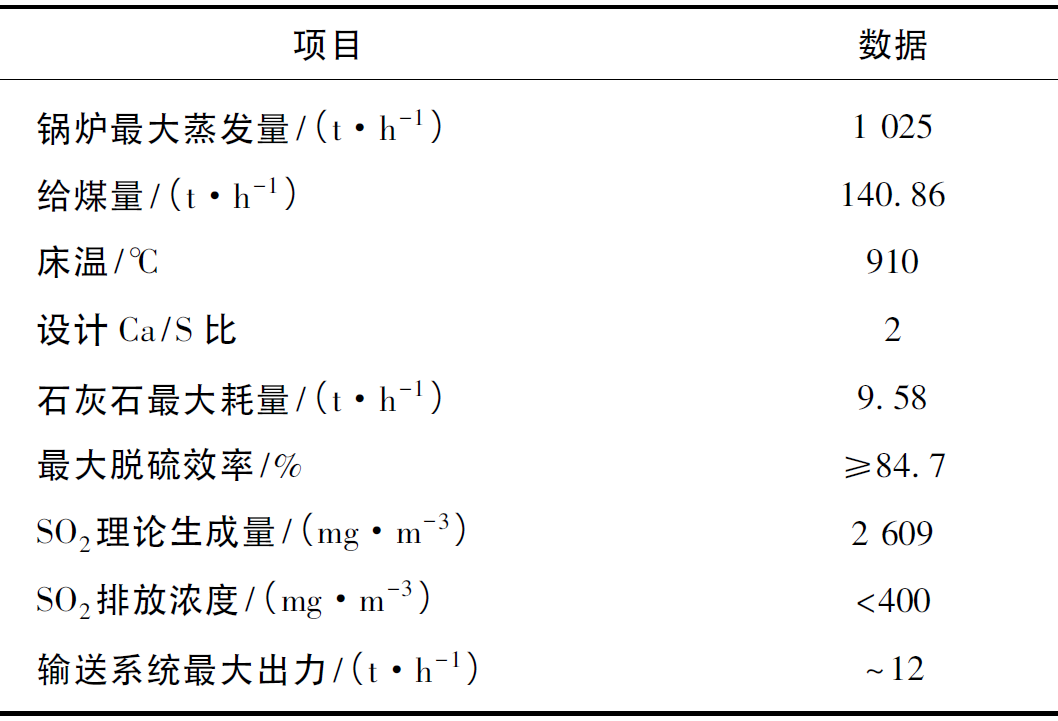
表4 烟气半干法脱硫系统主要参数
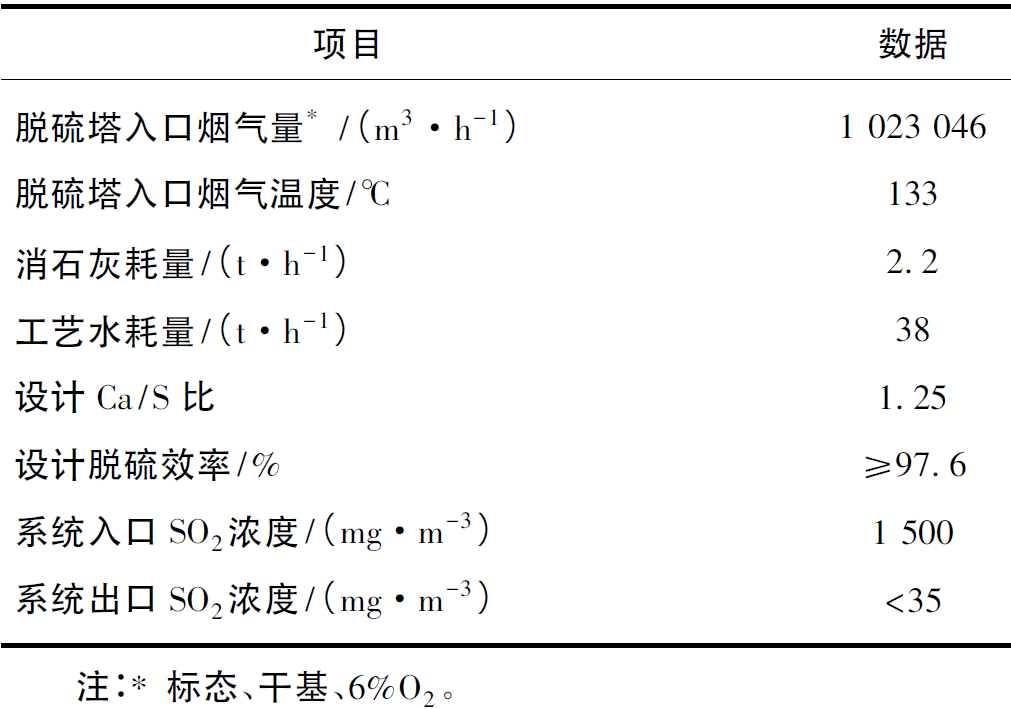
2016年9月两级脱硫系统主要运行参数见表5。表5表明:炉内干法脱硫平均Ca/S物质的量比1.82,综合脱硫效率达到73.33%;烟气半干法脱硫系统平均Ca/S物质的量比1.6,脱硫效率达到95.41%,总脱硫效率98.78%,SO2排放稳定,满足不高于35mg/m3的要求,两级脱硫系统出力均存在一定的裕量。脱硫塔入口SO2平均值516mg/m3小于设计值1500mg/m3,表明根据机组负荷等因素调整两级系统脱硫比例的匹配策略具有更优的SO2超低排放稳定性和运行经济性。
两级脱硫系统联合运行的结果显示:脱硫系统调节灵活性强,控制策略丰富。满足SO2超低排放的同时,取得了良好的经济效益和社会效益。值得注意的是一些CFB锅炉机组在进行脱硫系统改造时采用烟气脱硫工艺部分或者完全取代炉内干法脱硫工艺。由于CFB锅炉在设计时根据炉露点考虑一定的温度裕度设计尾部烟道低温受热面并布置除尘器及引风机等辅机系统,避免低温腐蚀。若降低CFB锅炉炉内干法脱硫效率或者炉内不脱硫,则由于烟气酸露点上升,会增加尾部低温受热面及相关辅机系统低温腐蚀的风险。
表5 两级脱硫系统主要运行参数
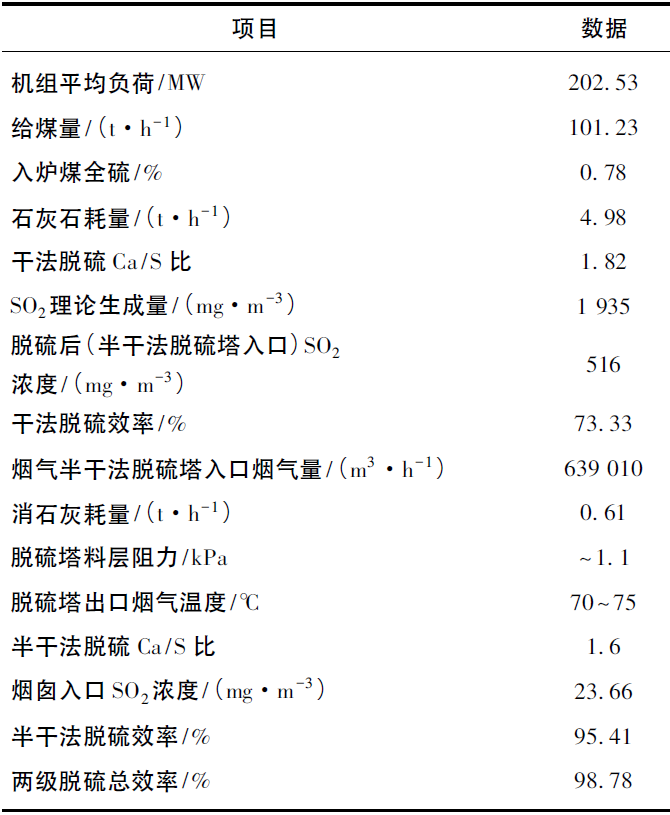
因此,CFB锅炉脱硫系统改造若需降低炉内干法脱硫效率时,应重新核算烟气的酸露点,以保证尾部低温受热面、除尘器和引风机等设备及烟道等部件的运行安全性。
4 结论
1) CFB锅炉SO2实际生成量取决于煤的硫分中可燃硫所占的比例、煤灰中CaO 等碱金属氧化物的含量,床温和过量空气系数等锅炉运行参数。
2) CFB锅炉通过降低SO2的生成量,炉内高效脱硫和烟气脱硫相结合的深度脱硫技术可以实现SO2的超低排放,并具有更高的调节灵活性和运行可靠性。
3) CFB锅炉烟气脱硫工艺的选取上,CFB-FGD半干法脱硫工艺相对于石灰石-石膏湿法脱硫工艺更具有经济优势。
4) CFB锅炉脱硫系统改造若需降低炉内干法脱硫的脱硫效率,应重新核算烟气的酸露点,以保证尾部低温受热面、除尘器和引风机等设备及烟道等部件的安全。