目前,排烟热损失占到了燃煤电站锅炉热损失总量的70%~80%,随着锅炉排烟温度的升高,机组发电煤耗也随之增加。研究表明,锅炉排烟温度每升高10℃,锅炉热效率将会降低0.5%~0.7%,机组整体发电煤耗将增加1.7~2.29g/kWh。
此外,排烟温度还是影响机组运行经济性和安全性的重要因素,锅炉排烟温度上升会造成湿法脱硫减温水量增加,烟气体积流量增大,飞灰比电阻增大,电除尘器效率下降,严重时除尘器滤袋还会出现高温氧化腐蚀。采用低压省煤器回收烟气余热,被认为是一项可降低排烟温度,提高燃煤机组热经济性的有效措施。
排烟余热可用来加热回热系统凝结水、一次风、热网水、干燥燃料,还可作为水媒式烟气加热器(MGGH)的热源。目前,应用较多的仍是利用排烟余热加热回热系统凝结水,排挤部分回热系统抽汽,返回汽轮机做功,提高机组热经济性。为配合某300MW CFB锅炉机组进行的超低排放改造,在锅炉尾部烟道内布置低压省煤器来降低排烟温度,并对设计方案进行优化以及热经济性分析。
1、机组概况
某电厂300MWCFB锅炉为上海锅炉厂有限公司制造,型号SG-1060/17.5-M802,亚临界中间再热、单锅筒自然循环。锅炉采用岛式布置、全钢构架悬吊结构,炉底采用水冷一次风室结构,炉膛采用气密式水冷壁,炉前布置两级破碎制煤系统,燃料由回料腿以及炉膛两侧墙给煤口进入炉膛。
锅炉实际运行排烟温度为140℃,为配合电厂进行的超低排放改造,拟在锅炉尾部烟道内布置低压省煤器。考虑燃用煤质以及低温腐蚀等因素,排烟温度降至120℃左右,排烟余热用于加热回热系统凝结水,回热系统如图1所示。锅炉设计燃用煤质数据见表1,回热系统主要参数见表2。
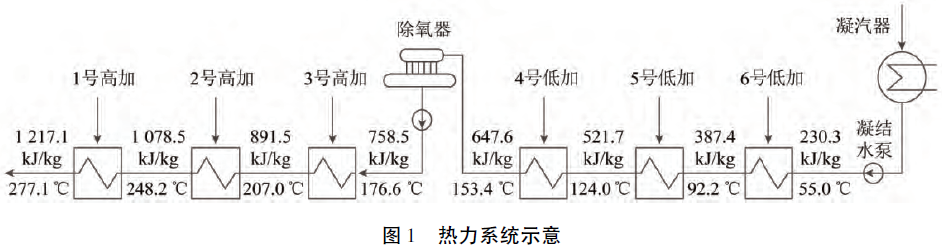
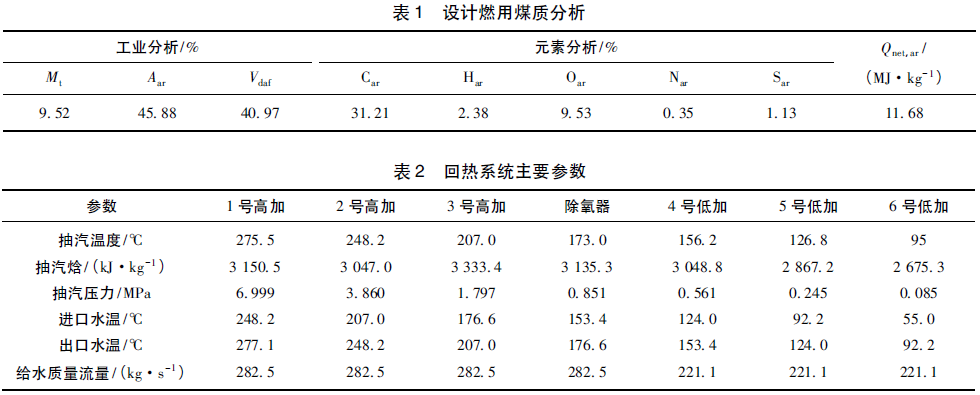
2、低压省煤器布置方案
低压省煤器一般布置于锅炉尾部烟道内,水侧与回热系统连接,通过吸收排烟余热加热回热系统凝结水,被排挤的部分抽汽,返回汽轮机中继续做功。增设低压省煤器后,可以保证机组在燃料投入量不变的情况下,提高机组热经济性。
2.1烟气侧布置方案
表3为低压省煤器布置方案的优缺点。由表3可知,方案2和方案4在有效利用排烟余热的同时,可提高电除尘效率,减少脱硫减温水量。由于本次改造排烟温度降幅在20℃左右,采用布置方案2较为合理。
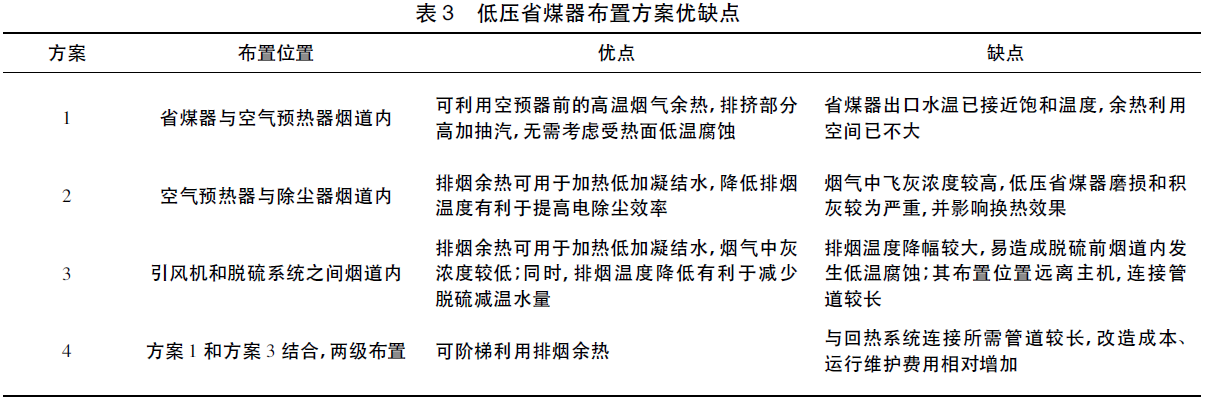
2.2与水侧连接方案
低压省煤器与水侧连接方案主要有串联和并联2种。相比于串联系统,并联系统无需增加凝结水泵的压头,采用级间压降即可保证低压省煤器内凝结水流动。因此,低压省煤器系统与回热系统一般采用并联。
2.3受热面管型选择
低压省煤器受热面可选用光管、螺旋肋片管和H型翅片管。相比于光管,螺旋肋片管和H型翅片管换热面积较大、传热性能较好。对于除尘器之前的换热器,烟气中灰浓度较高,螺旋肋片管易磨损和积灰,采用H型翅片管较好;对于引风机之后的换热器,由于经除尘器后烟气中灰浓度极低,可采用换热效率更高的螺旋肋片管。此外,在相同条件下,顺列管束最大磨损量较错列管束少3~4倍。因此,采用顺列布置可减轻烟气对管束的磨损。
3、方案设计
3.1方案设计原则
低压省煤器布置在锅炉尾部烟道内,烟温降幅应结合实际排烟温度以及燃用煤中硫分,确定烟气酸露点温度,防止排烟温度过低,腐蚀受热面和除尘器滤袋。由于除尘器前烟气中飞灰浓度较高,易对受热面造成磨损,影响低压省煤器使用寿命。因此,方案设计要遵循以下原则:
1)防腐原则。由于烟气侧对流放热系数远小于水侧,管壁温度与水温接近。若省煤器入口水温偏低,进口管壁温度接近水露点温度,易造成受热面严重低温腐蚀。因此,应根据燃用煤种来确定最低允许壁温并合理控制入口水温,以保证管束最低壁温高于水露点25℃以上,避开严重低温腐蚀区。
2)防磨原则。除尘器前烟气具有飞灰浓度较高、流速较快的特点,由于管壁磨损量与烟气流速以及烟气中飞灰浓度成正比,若低压省煤器布置于除尘器前,应考虑受热面磨损问题,采取防磨措施。
3)强化传热原则。由于省煤器后尾部烟道内剩余空间较为紧凑,为降低排烟温度需适应烟道几何尺寸,必要时应采取强化换热的措施,来提高换热效率。同时,还应考虑烟道阻力增加对引风机出力的影响。
3.2设计方案提出
当考虑低温腐蚀问题时,低压省煤器进出口采用“两点取水,一点回水”的水温调节方式,即由低压加热器引出2路不同温度凝结水,通过调节2路凝结水的混合比例,可避免低负荷下低压省煤器入口水温过低,出现低温腐蚀。由于设计低压省煤器布置于除尘器前,烟气中灰浓度较高,综合考虑烟道可利用空间、烟气侧增加的流动阻力以及积灰和磨损,低压省煤器管束采用H型鳍片管顺列布置较为合理。由表2可知,4号低加抽汽温度为156.2℃,4号低加出口水温为124.0℃,表明排烟余热只能用于加热4~6号低压加热器之间凝结水。因此,提出3个低压省煤器方案进行烟气余热的回收,具体连接方案如图2所示。
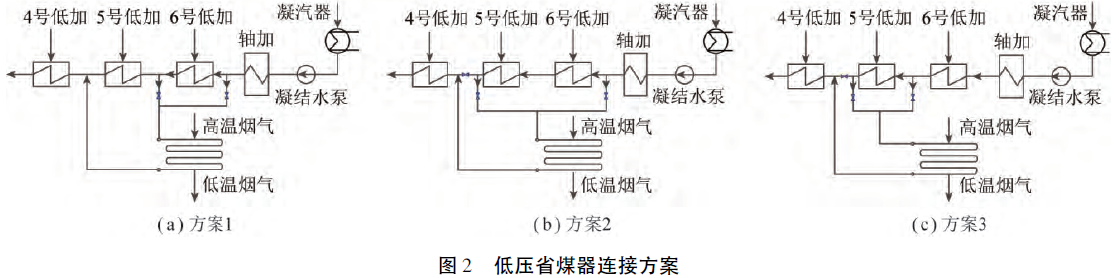
方案1:分别从6号低压加热器的进、出口取水汇集后,引入低温省煤器入口,再从低温省煤器出口引至5号低压加热器的出口;方案2:分别从6号低压加热器的进口和5号低压加热器的出口取水汇集后,引入低温省煤器入口,再从低温省煤器出口引至4号低压加热器的进口;方案3:分别从5号低压加热器的进、出口取水汇集后,引入低温省煤器入口,再从低温省煤器出口引至4号低压加热器的进口。
当排烟温度由140℃降至120℃时,单位烟气焓降为117.7kJ/kg,燃煤量为245.7t/h,烟气的总焓降为29133.4kJ/h。根据热平衡理论,低温省煤器吸收排烟余热30794.58kJ/kg。额定负荷下,各方案经济性计算结果见表5。由表5可知,方案3机组热经济性较高,发电煤耗降低相对较多,为最佳方案。机组运行按照每年4000h计算,选用方案3,可使发电煤耗降低1.371g/kWh,年节省标煤量为1820.173t,减排二氧化碳2082.945t,可有效提高机组的热经济性。
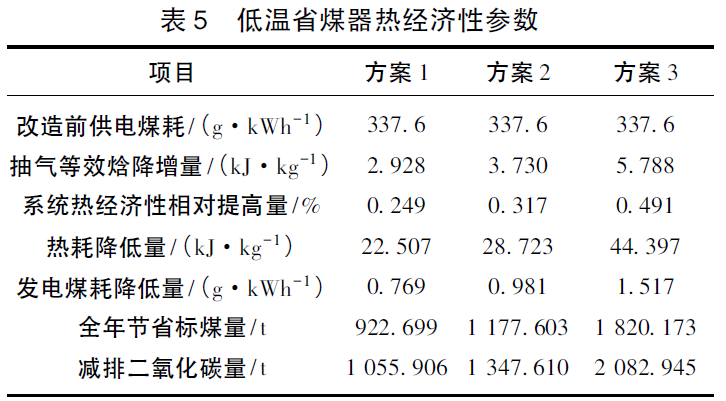
4、结论
1)针对某电厂排烟温度较高的问题,结合电厂需进行超低排放的实际情况,将排烟温度由140℃降至120℃,回收的烟气余热进入回热系统,从而提高机组经济性。
2)根据低压省煤器系统设计的原则及参数要求,通过优化设计,确定在空气预热器与除尘器之间顺列布置H型鳍片管省煤器,提出3个布置方案,并对方案的热经济性进行分析。
3)结果表明,方案3的热经济性较高,可使发电煤耗降低1.371g/kWh,年节省标煤量为1820.173t。